General Capabilities
The MARS computational framework for performing Multiphysics Analyses of the Response of Structures has a number of unique features that make it one of the most versatile and powerful platforms available.
Most commercially available computational frameworks are built around a specific discretization scheme and solution algorithm, thus limiting the range of applications and ability to deal with emerging computational challenges and approaches. Furthermore, customization of available constitutive models, element formulations, contact conditions or solvers is typically quite limited, necessitating the use of external scripts to extend capabilities. The latter, if even possible, leads to significant performance reductions.
MARS on the other hand has been developed in a modular way, making use of the computational efficiency but also core capabilities of the object-orientated coding language C++ such as abstraction, encapsulation, inheritance, and polymorphism. This makes it possible to seamlessly integrate different discretization schemes, constitutive models, contact conditions, and solvers.
MARS, thanks to its object-oriented architecture, makes it possible to add new capabilities in an efficient and systematic fashion, even for end-users, without restrictions regarding the type of capability. In addition to user-defined elements and materials, users can also integrate alternative solvers, optimization algorithms, visualization schemes, automatic model generation and post-processing schemes, or probabilistic features.
MARS features some unique techniques which facilitate the solution of problems involving structural break-ups, fragmentation, and post-failure response under extreme loading condition. As such, MARS has been successfully adopted for the simulation of a wide variety of problems, which include:
- Modeling of cracking and failure of quasi-brittle and heterogenous materials
- Response of structures to blast loads and fragment impacts
- Cable dynamics problems
- Laceration and fragmentation of plates and shells
- Modeling of the breakup and failure of textile composite structures
In addition to the solution of mechanical problems in the static and highly dynamic domain, MARS also supports multi-physics analysis with one-way or two-way coupling between mechanical and multi-physics problems. Some of the capabilities include but are not limited to:
- Exothermal curing reaction of cementitious and polymeric materials
- Cure-dependent mechanical response of cementitious materials and thermoset polymers
- Drying-shrinkage
- Rate-type creep analysis
- Cracking and self-healing of cementitious materials
- Deterioration due to alkali-silica reaction (ASR)
- Spatial variability through random fields
- Prestressing steel relaxation
- Steel and macro-synthetic short fiber reinforcement
MARS offers the most suitable and powerful tools in single package for solving some of the most challenging problems in engineering such as FEM-based analysis of thermal warping and hygral shrinkage of bridge girders, the heterogenous response of continuous fiber reinforced composites, as well as time-dependent response of concrete in the fresh and hardened states.
Discretization Schemes
While MARS includes all the capabilities and versatility expected from a general finite element code, MARS is not limited to these capabilities. What makes MARS powerful is the fact that within a single framework, one can access the continuum finite element method (FEM), novel material specific discrete discretization schemes, and the traditional Discrete Element Method (DEM).
Examples of the novel discrete discretization schemes that reproduce the intrinsic heterogeneity of the materials are e.g. LDPM for concrete and DM4C for composites. The discrete element method (DEM) can be used to e.g. model the flow of concrete in its fresh state during pumping and deposition while interacting with hardened concrete represented by either FEM or LDPM.
Owing to the goal of simulating structural response past the point of stability loss and collapse, MARS is based on dynamic explicit algorithms although also implicit solvers are available which can be used side by side.
Some of the element formulations that are available within MARS and that are well-suited to modeling the response of structures in the fresh state as well as past the breaking point and, thus, to investigating structural failure modes are:
- DEM elements
- QPH quadrilateral shell elements with physical hourglass stabilization;
- DKT triangular shell elements;
- Beam elements with various built-in cross sections;
- 8-Node Flanagan-Belytschko hexahedral elements with hourglass stabilization;
- Hyper-elastic solid elements;
- Various constraint formulations, including concrete-rebar interaction;
- Automatic contact algorithm for node-face, edge-edge, node-edge, node-node contact detection;
- Macro-particles for simulating discrete elements with complex shapes;
- The Lattice Discrete Particle Model (LDPM), the most comprehensive tool in the market for the discrete simulation of quasi-brittle concrete and rocks;
- The DM4C for composites
- A fluid structure interaction (FSI) interface with the Eulerian software GEMINI for the simulation of blasts and explosions.
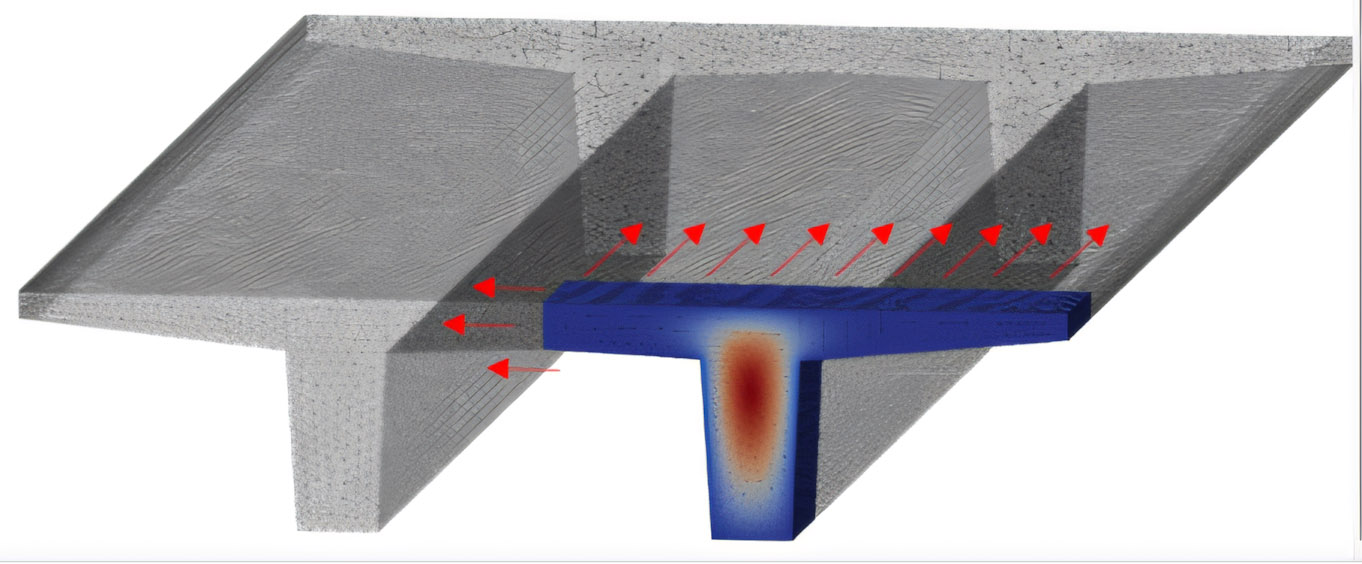
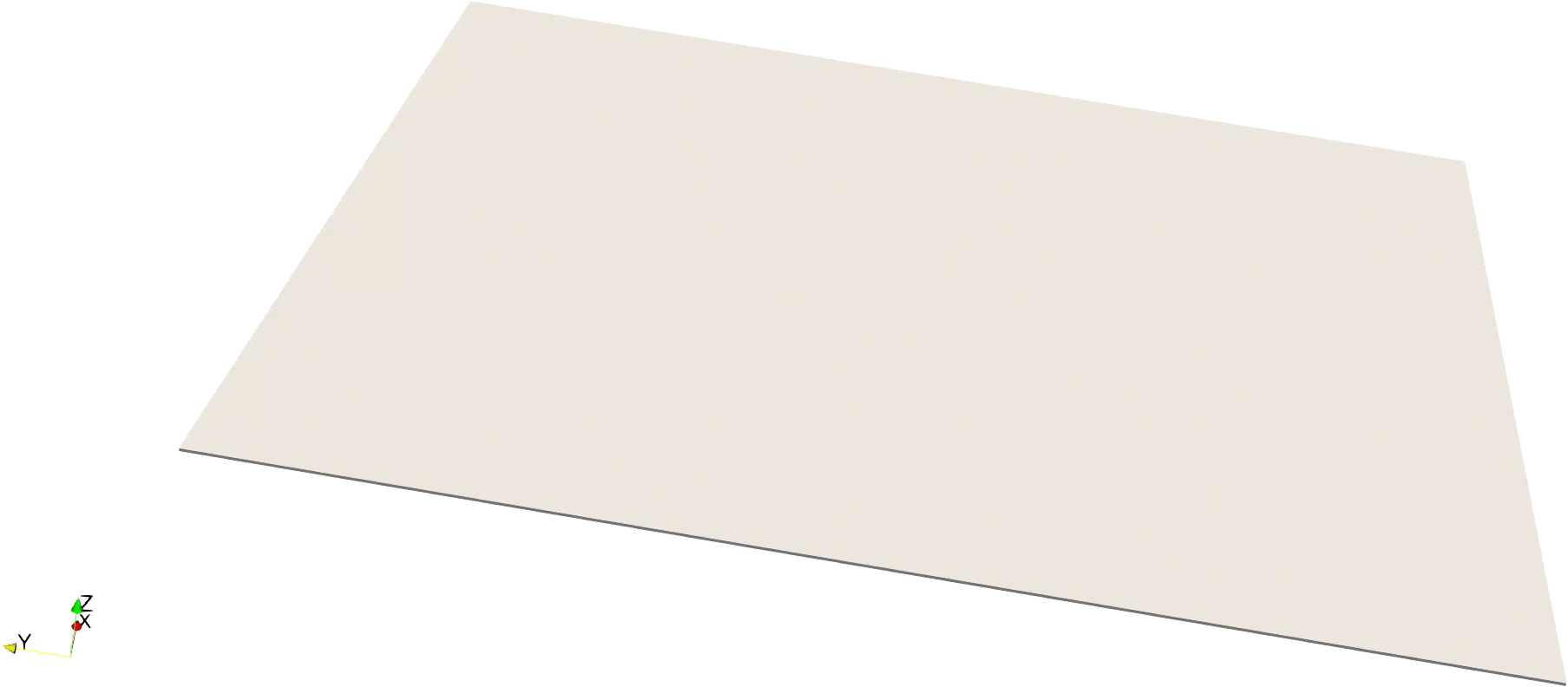
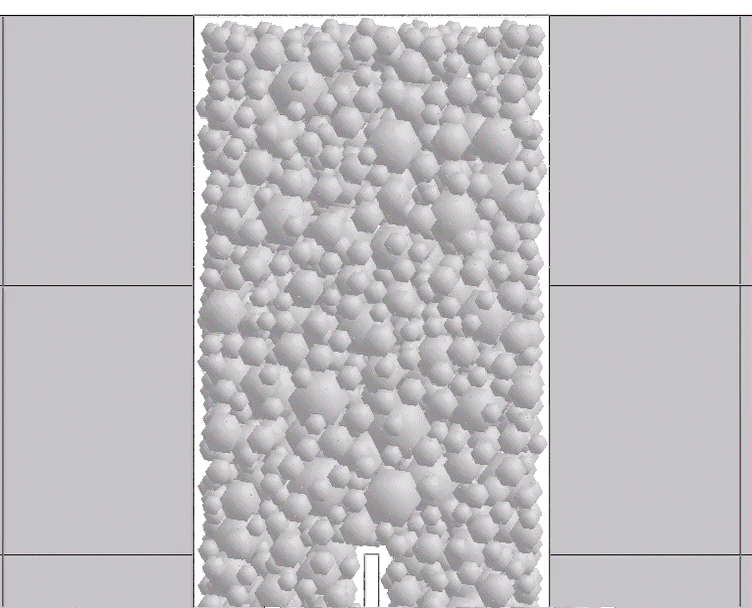
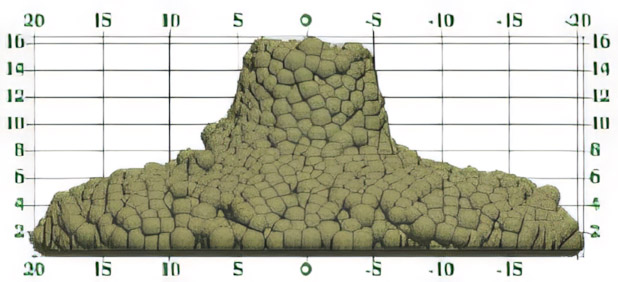
Constitutive Models
In addition to a multitude of different discretization options available in a single fully integrated framework, MARS also offers a range of different constitutive models that are well-suited for the analysis of plastic as well as quasi-brittle materials considering rate-dependent material characteristics.
These include more traditional tensorial model formulations but also models formulated by means of vectorial constitutive equations.
Available tensorial constitutive models include:
- Elastic
- Elasto-plastic
- Rate-dependent elasto-plastic
- Iso-tropic damage
- Johnson-Cook Model
- Drucker Prager
- Grassl-Jirasek damage plasticity model v1 and v2
Vectorial constitutive models
- Microplane model M4 for FEM analysis of concrete structures
- Microplane model M7 for FEM analysis of concrete structures
- Microplane model for unidirectional composites
- Microplane model for two-dimensional composites
- Lattice Discrete Particle Model (LDPM)
- Discrete Model for Composites (DM4C) for continuous fiber reinforced composites
Depending on the acceptable computational cost and the required accuracy of the results, different microplane versions with 21, 28, 37 or 61 microplanes are available.
Additive Manufacturing (AM)
Additive manufacturing (AM) is quickly gaining traction in many areas of engineering including for example. 3D printed concrete (3DPC) in structural engineering, metal sintering or additively manufactured composites.
A successful introduction of additive manufacturing requires predictions not only of buildability but also of long-term performance affected by a number of mechanical and environmental influence factors. The performance of an additively manufactured structure is anchored in the early printing process due to resulting geometrical imperfections, introduced defects, time-dependent mechanical properties and imprinted thermal and hygral eigenstrains that only in part are relaxed due to the visco-elastic/ visco-plastic behavior of many of the involved materials.
Modelling additively manufactured structures: (a) g-code based definition of print path, (b) deposition of fresh concrete modeled through DEM, (c) FEM based representation of hardened 3D-printed concrete.
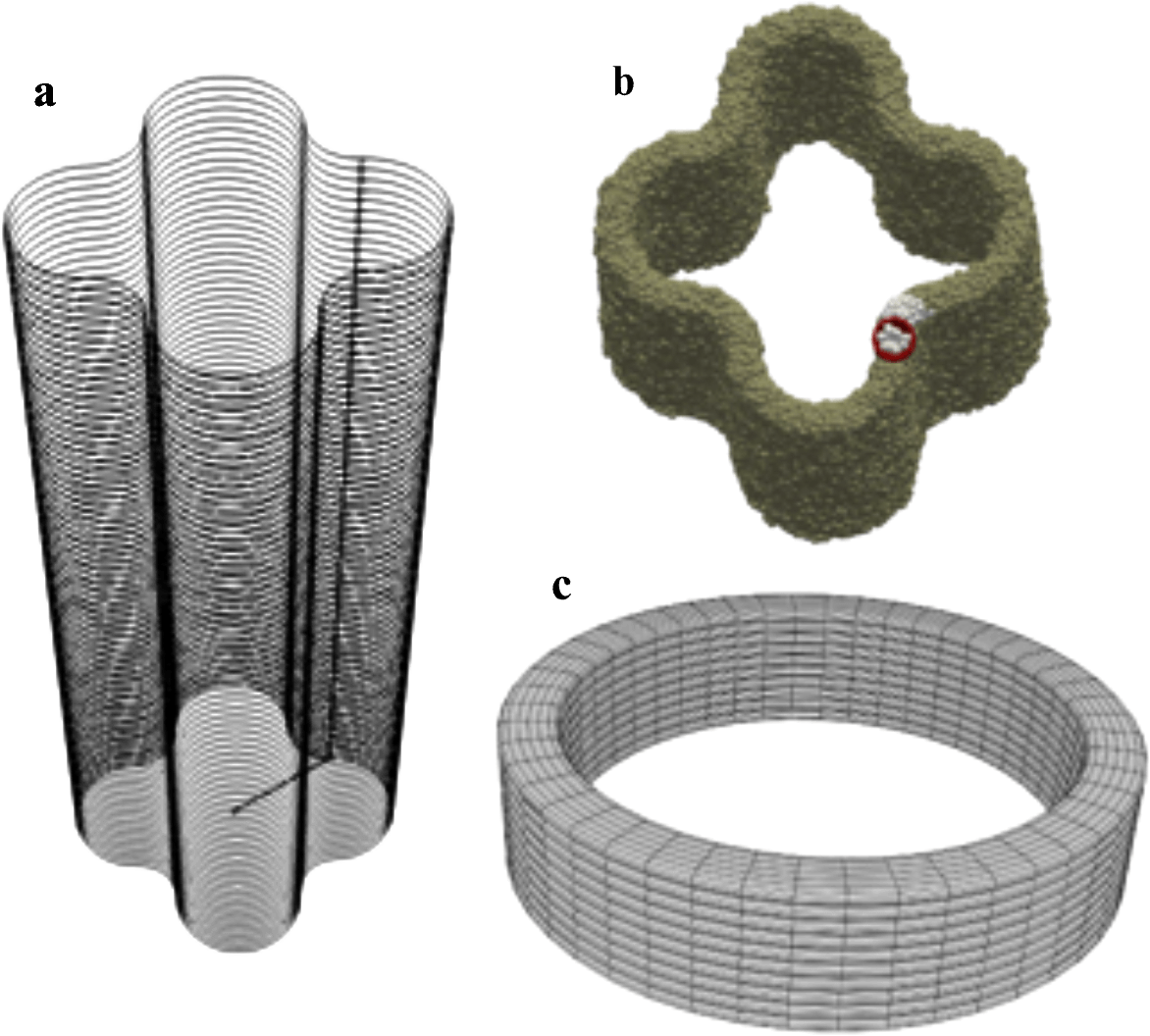
MARS supports modeling of the print-path dependent deposition of material (the actual printing process) as well as the analysis of printed structures in the hardened state. The direct support of g-code based printing instructions simplifies the model generation while different discretization approaches cater to different applications. MARS includes both a DEM-based approach for the modeling of pumping and material deposition and a more traditional FEM-based approach to model the behavior of the hardening / hardened structure early after formation and beyond. For the latter analyses many tools are readily available such as for example cure-dependent constitutive models and modules for the prediction of thermal and hygral strains taking into account visco-elastic deformations.
MARS has a Discrete Model for Composites (DM4C) that explicitly simulates tow deposition and matrix polymerization for continuous-fiber composite AM. DM4C uses an ultra-high-fidelity description of bond formation and manufacturing defects such as tow waviness, instabilities, porosity, and inter-filament debonding. DM4C captures the viscous and frictional phenomena between tows with a physics-based model, making the simulation of damage (such as microcracks, de-laminations, and cavitation) possible.
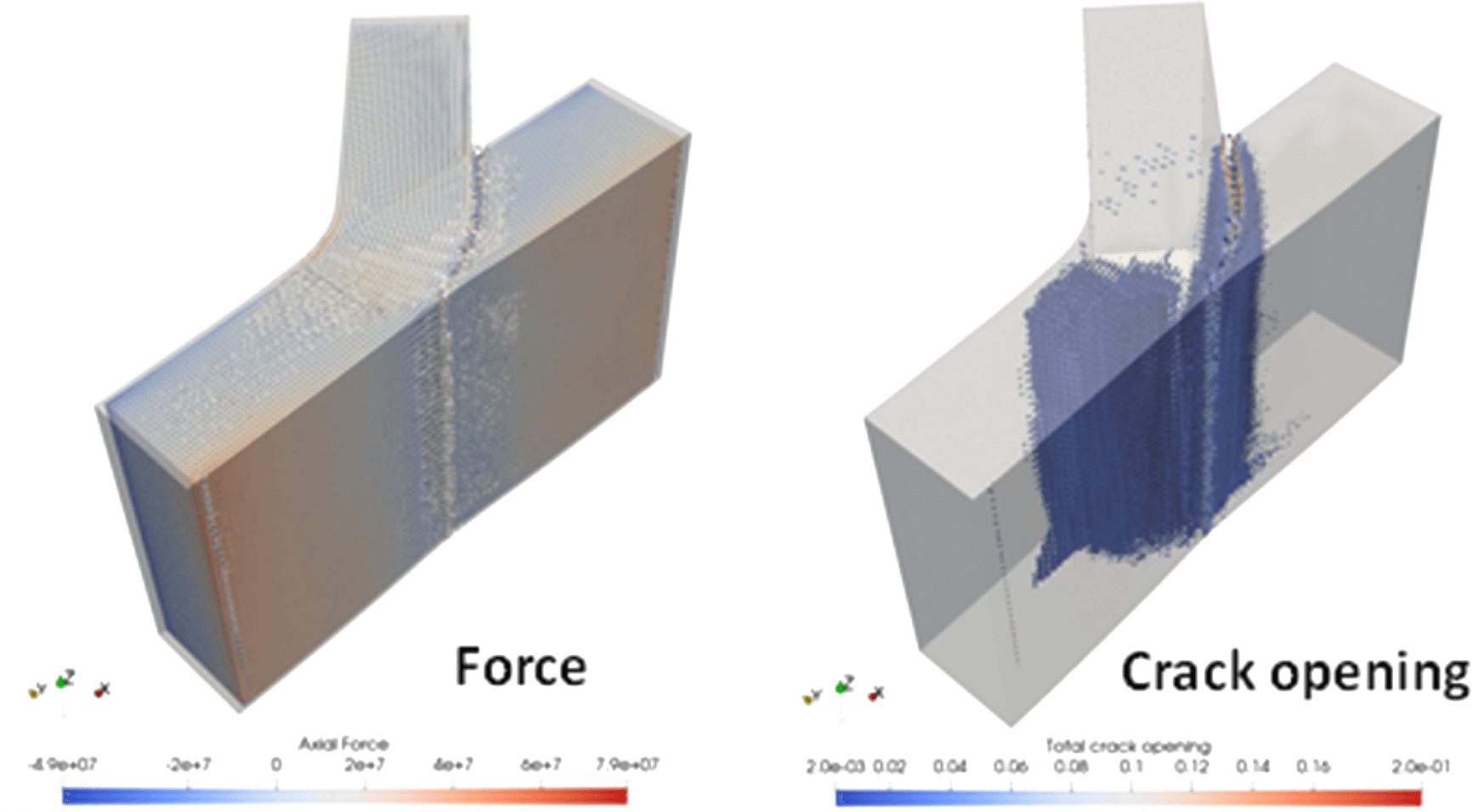
Digital Twins
The optimal design and manufacturing of additively manufactured (composite, 3DPC) structures requires extensive parameter explorations to identify tradeoffs between manufacturability and performance, along with correcting possible issues before production. Traditionally, this process requires extensive physical trial and error resulting in slow product development, large costs, and a significant increase in the time from conception to qualification. MARS enables the Digital Engineering (DE) of the build process. Using digital data instead of experiments allows for the identification of possible problems early in the project when costs for corrective measures can be hundreds of times lower than after production has started. At the same time, digital manufacturing allows one to explore various combinations of manufacturing parameters that lead to optimal quality and repeatability in a short amount of time.
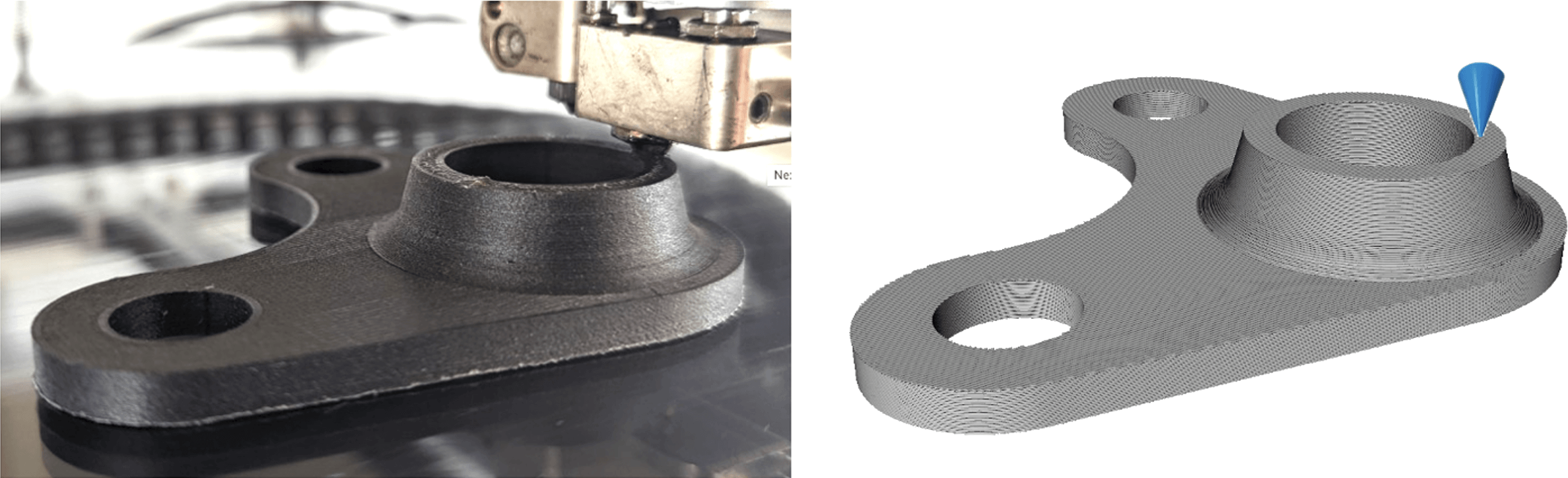
Finding an optimal design is of course not limited to AM applications and represents an area of interest in many fields of engineering including structural concrete. A good Digital Twin requires a digital representation of the salient features of a given structure or problem. MARS is in the unique position to reproduce the heterogeneity of concrete through LDPM, predict the cure-dependent response of concrete in a coupled analysis in which also thermal and hygral strains and creep-deformations can be captured.
Digital Twinning of concrete structures is not only interesting for the development and optimization of new structures but can also serve as a powerful analysis tool. While of tremendous importance, destructive and non-destructive structural testing offer only limited insights into the structural response – typically restricted to global forces and deformations, and individual strain components in points. Digital image correlation and other methods have improved the quality of information that can be obtained in experiments, which however remains limited. Digital Twins of laboratory tests overcome these shortcomings by giving access to all desired deformation and stress quantities after calibration and validation. Virtual testing is yet another area of application for advanced models.
Engineering Nonlinear Analysis
The wide range of available discretization methods and constitutive models in combination with powerful solvers and an attractive licensing model make MARS an interesting choice for advanced structural analysis tasks, especially if distributed damage, nonlinear behavior or time-dependent aspects are of importance.