Independent ISO 17025 Lab Testing
ISO 17025 is an internationally recognized laboratory test standard and the authoritative standard for demonstrating laboratory test competence. ES3’s Georgia Technical Operations Center (GTOC) located in Warner Robins, Georgia maintains a certificate of accreditation in ISO17025 testing, enabling us to demonstrate that we:
- operate with competency and consistency across equipment, technicians, scientists, and engineers, and
- generate accurate and valid test results.
ES3 has the ability to perform testing on eight (8) different tests in accordance with the American Society for Testing and Materials (ASTM) standards.
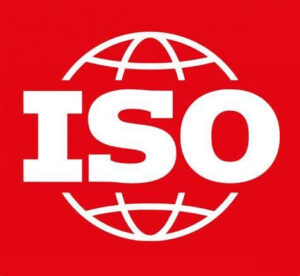
Hydrogen Embrittlement (ASTM F519)
Hydrogen embrittlement (HE) is a form of corrosion common among high strength steels (HSS). HE is especially common after immersion in chemicals and after undergoing various electrochemical processes. HE testing involves imparting a sustained load on a precisely machined specimen with a known fracture structure strength of a machined notch. The test typically requires maintaining the sustained load at a certain percentage of the notch fracture strength for 200 hours. If the process the test specimens underwent did not cause embrittlement, then the coupons should last the full 200-hour duration. ES3 routinely accomplishes HE testing for customers by showing no embrittlement took place after surface finishing with one of ES3’s technologies, such as low hydrogen embrittlement alkaline zinc-nickel (LHE alkaline Zn-Ni).
Root cause failure analysis showing HE failure on a Scanning Electron Microscope (SEM).
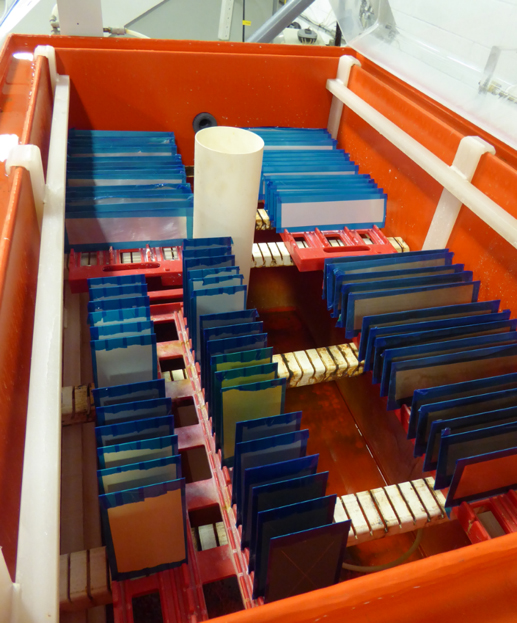
Panels set up with ASTM B117 salt fog corrosion chamber at GTOC.
Salt Fog Corrosion (ASTM B117)
Salt fog corrosion is a form of expedited corrosion testing whereby test panels are placed in a salt fog chamber to determine corrosion resistance. This testing can be performed on a variety of coatings including metallic, inorganic, and organic. ES3 routinely performs salt fog corrosion testing in accordance with ASTM B117 and this testing is audited by Nadcap as part of ES3’s LHE alkaline Zn-Ni plating line. ES3 has 3 salt fog corrosion chambers at the (GTOC) capable of performing salt fog corrosion testing.
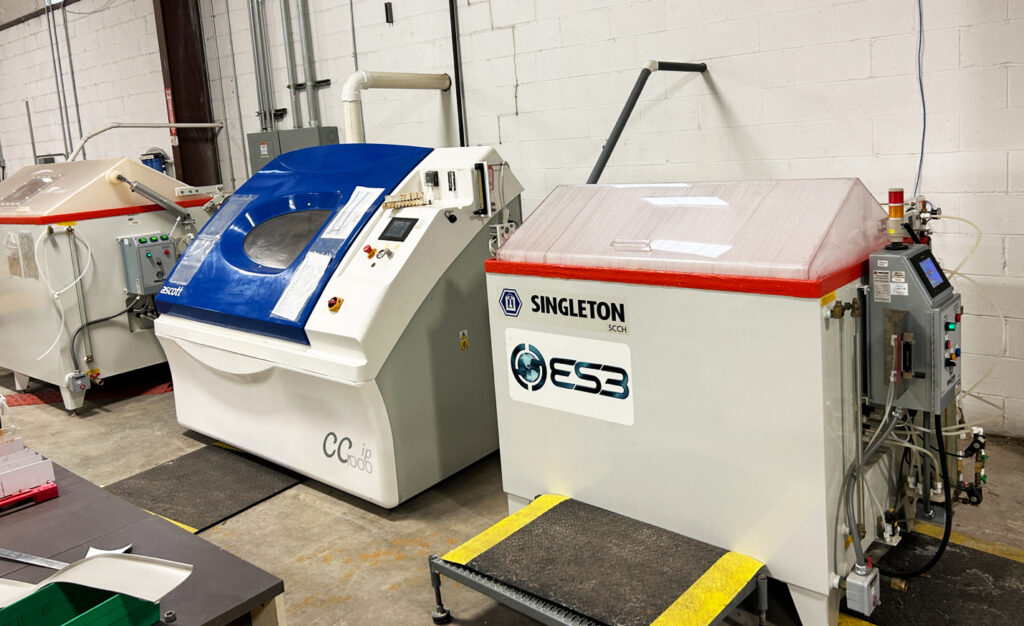
Three salt fog corrosion chambers at the GTOC.
ASTM E384 and ASTM B578 Hardness Testing
Hardness testing is a way to characterize material’s wear resistance by making small indentations and measuring the resulting forces or distances. Hardness testing can be performed on almost any range of materials and/or coatings and yield accurate, repeatable results. ES3 performs Vickers microhardness testing per ASTM E384 to measure the hardness of coatings produced from their additive manufacturing technologies like Cold Spray and High Velocity Oxygen Fueled (HVOF) coating.
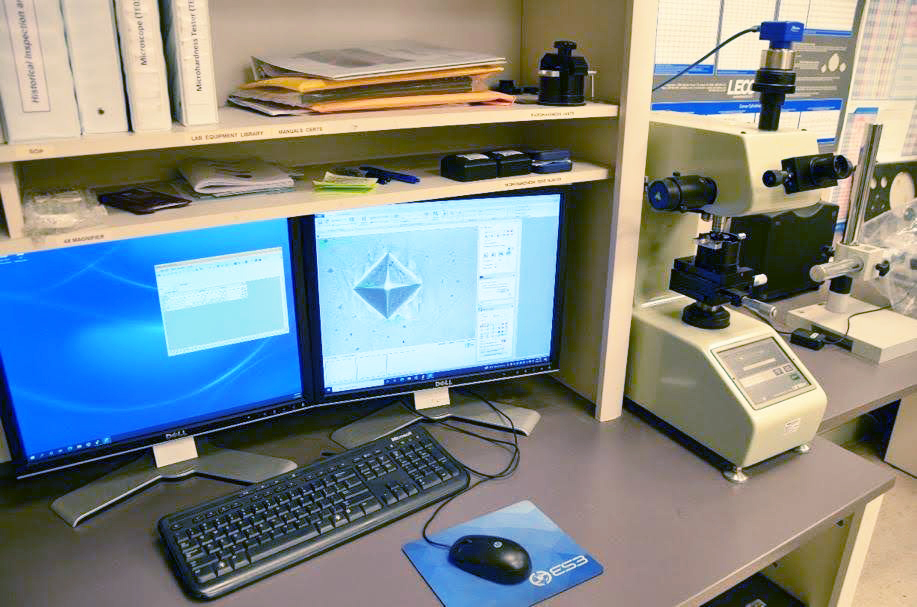
ASTM E384 Vickers microhardness measurement being taken on a sample.
ASTM E8 Tensile Testing
Tensile testing is accomplished by pulling a sample at a set rate until fracture while tracking stress and strain over time. This results in a stress-strain curve, which can provide many material properties, such as yield strength, ultimate tensile strength, elongation, Young’s Modulus, and more. ES3 uses ASTM E8 tensile testing to both qualify material lots for sample/part manufacturing, and for comparing legacy processes to novel technologies like Laser Assisted Cold Spray (LACS).

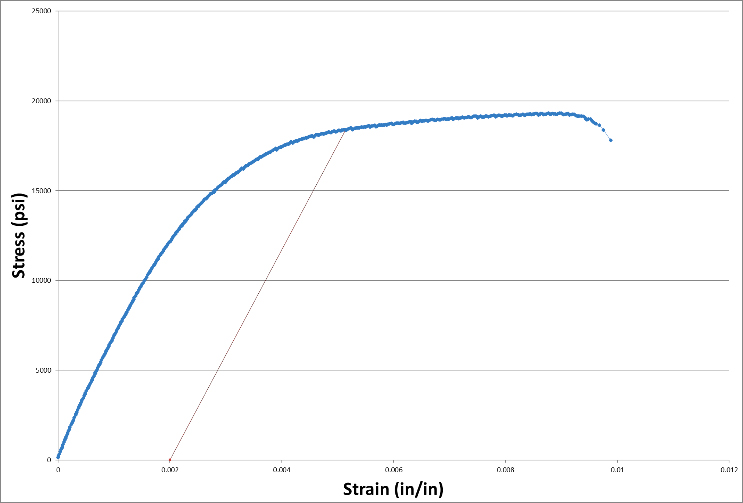
ASTM E8 tensile test with extensometer to record strain (left) and a tensile curve from a completed test (right).
ASTM E466 Fatigue Testing
Fatigue testing is a form of accelerated cyclic testing performed on samples representing actual parts. Samples are rapidly cycled in a sinusoidal force wave between an upper and lower force depending on the stress ratio and stress level chosen. The results are plotted on a cycles vs. stress curve, and they can be used to predict the fatigue life of parts at interpolated stresses. ES3 uses ASTM E466 fatigue testing to compare the fatigue effects of legacy processes like grinding and plastic media blast to new processes like the Pulse Automated Water Strip System (PAWSS). ES3 has three 55,000 pound servo hydraulic test machines and two 20,000 pound servohydraulic test machines at the GTOC.
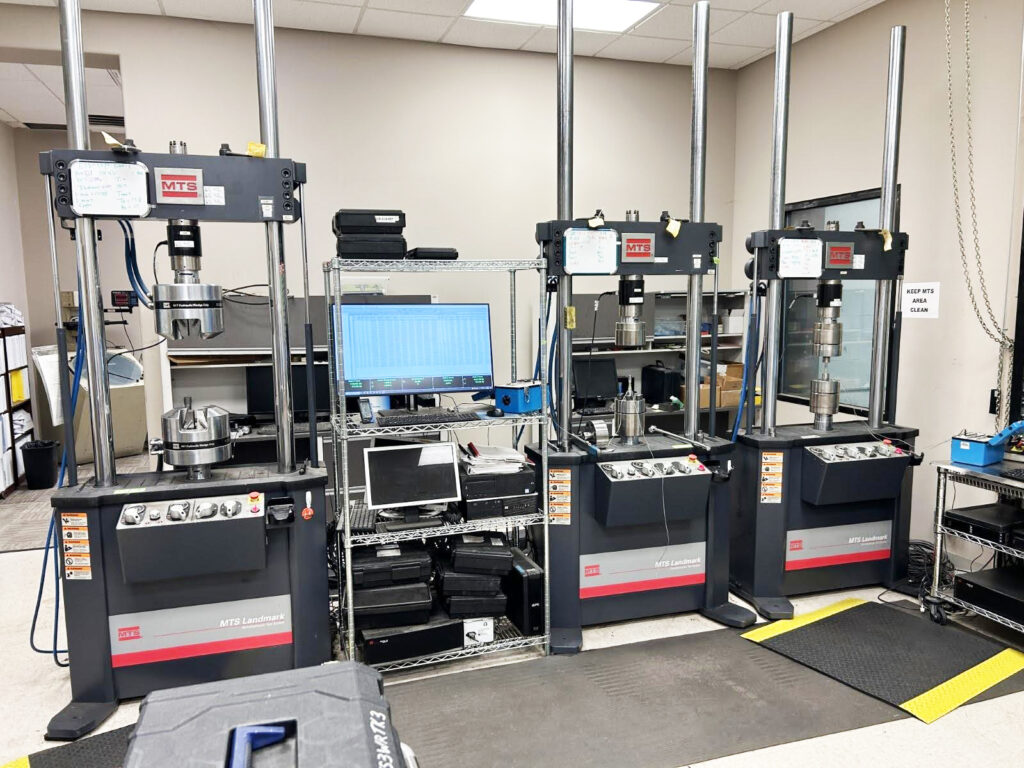
GTOC servo hydraulic testing machines with flat coupon grips installed for ASTM E8 tensile testing (left) a sample in the installation process (middle) and an ongoing ASTM E466 fatigue test (right)e.
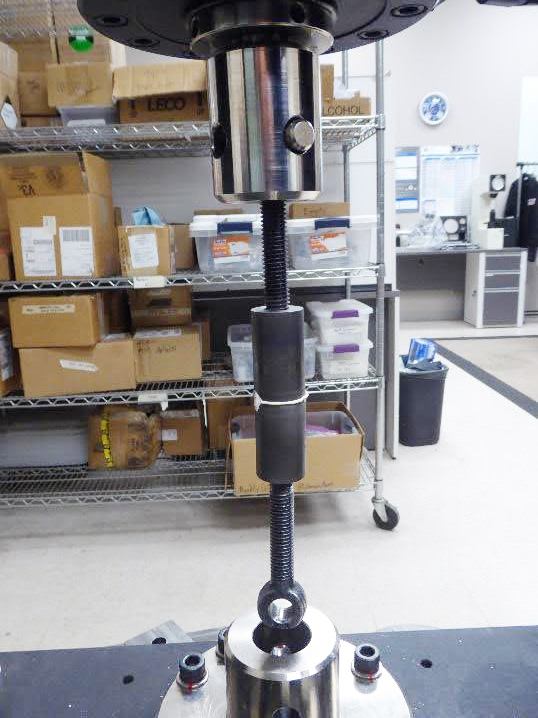
ASTM C633 bond strength sample being loaded.
ASTM C633 Bond Strength Testing
ASTM C633 bond strength testing is a pull test similar to ASTM E8 tensile testing, where a thermal sprayed sample is cleaned, glued to a blank sample, and then pulled by a tensile force until fracture. A set displacement rate is used, like in some ASTM E8 tensile tests. The resulting bond strength measurements per ASTM C633 determine if a lot of HVOF or Cold Spray powder and spray parameters can be qualified for use. By observing the fracture surface, ES3 determines whether fractures are cohesive or adhesive, and can then adjust spray application parameters to improve results.
ASTM B571 Adhesion Testing
Adhesion testing is used to determine the ability of a coating to stay adhered to a substrate material. ES3 uses the ASTM B571 Impact Test followed by the ASTM B571 Chisel-Knife Test. A 5mm ball nose tupp is dropped from a specified height twenty five times on one inch square areas of a five inch square coupon. Then, a cold chisel is used to attempt to pry up coating. Cold Spray coatings without connections between the impacts pass the test. ES3 also uses this test understand the impact performance of their sprayed coatings.
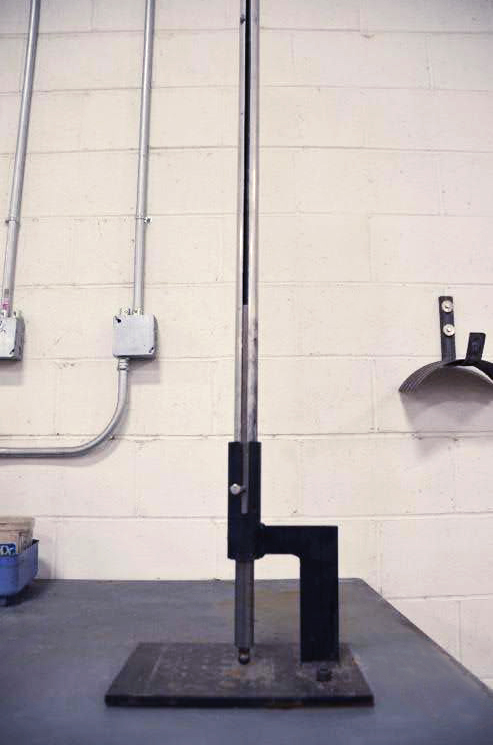
ASTM B571 Impact Test Apparatus.
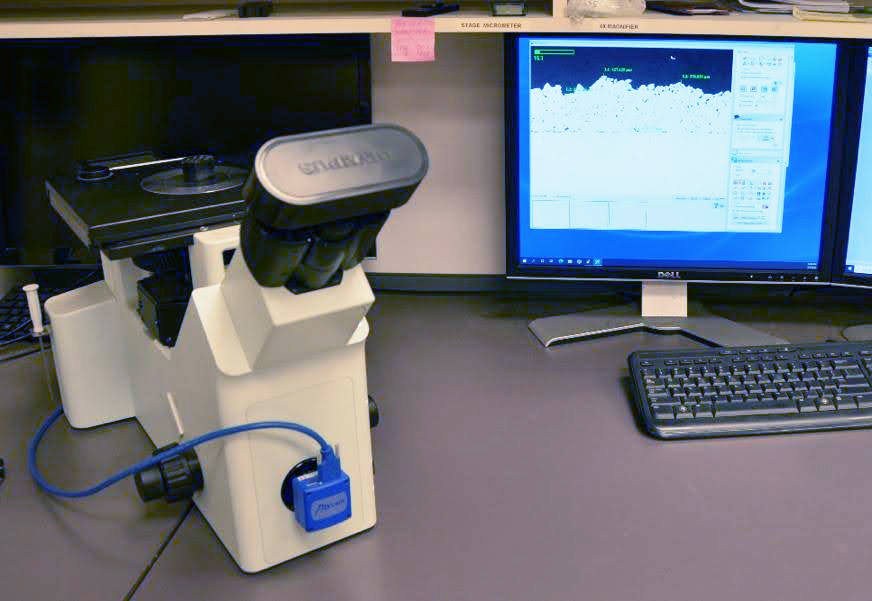
Microscope and coating thickness measurement system.
ASTM B487 Metal Oxide Thickness Testing
Coupons are coated using a thermal spray process and then cut, mounted, grinded, and polished. A polished sample is then placed under a microscope where ten thickness measurements are taken and averaged to give the sample coating thickness. Taking measurements under a microscope eliminates potential edge effects and coating thickness variability that would affect results from other measurement methods.