Cadmium Replacement
Zinc Nickel as an Environmentally Preferred Alternative to Cad Plating
Low Hydrogen Embrittlement (LHE) Cadmium (Cd) Plating per MIL-STD-870 is currently used as a sacrificial protective coating on high strength steel (HSS) aircraft landing gear components to prevent corrosion. The Environmental Protection Agency (EPA) and DoD strictly regulate Cd waste streams and personnel exposure. Aircraft manufacturers and overhaul facilities have received waivers to continue use of Cd because there has not been a technically feasible 100% substitute for Cd plating. High strength steels used in landing gear pose unique challenges due to their sensitivity to Hydrogen Embrittlement (HE) and Environmentally-Assisted Cracking (EAC).
ES3 has developed, qualified, and implemented LHE alkaline Zinc-Nickel (Zn-Ni) Dipsol IZ-C17+ plating on high strength steels which meet Cd plate baseline corrosion prevention, fatigue, and HE objectives. This LHE Zn-Ni process enables aerospace manufacturing to meet environmental restrictions by eliminating Cd waste streams. Zn-Ni is a cyanide free plating process that meets the requirements for a non-embrittling process per ASTM F519. The LHE Zn-Ni process has excellent throwing power in both plating and corrosion protection. The coating consists of a uniform zinc alloy containing 12-18% nickel. LHE Zn-Ni is applicable to aircraft major structural components, such as pistons, cylinders, truck beams, torque arms, and axles as well as consumables such as pins, bearings, bushings, and bolts.
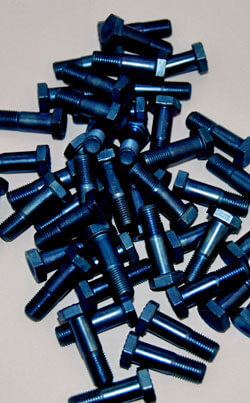
LHE Zn-Ni coated bolts that were barrel plated in the LHE ZnNi line.
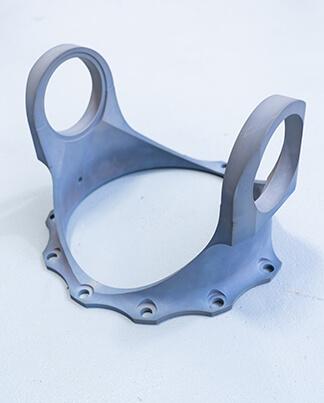
ES3 operates our own LHE Zn-Ni plating line where we plate components made in-house and components sent to us from other manufacturers. Additionally, ES3 performs barrel plating of nuts, bolts, and fasteners. For more information about our LHE Zn-Ni plating services, please contact us at ZnNi.plating@es3inc.com.
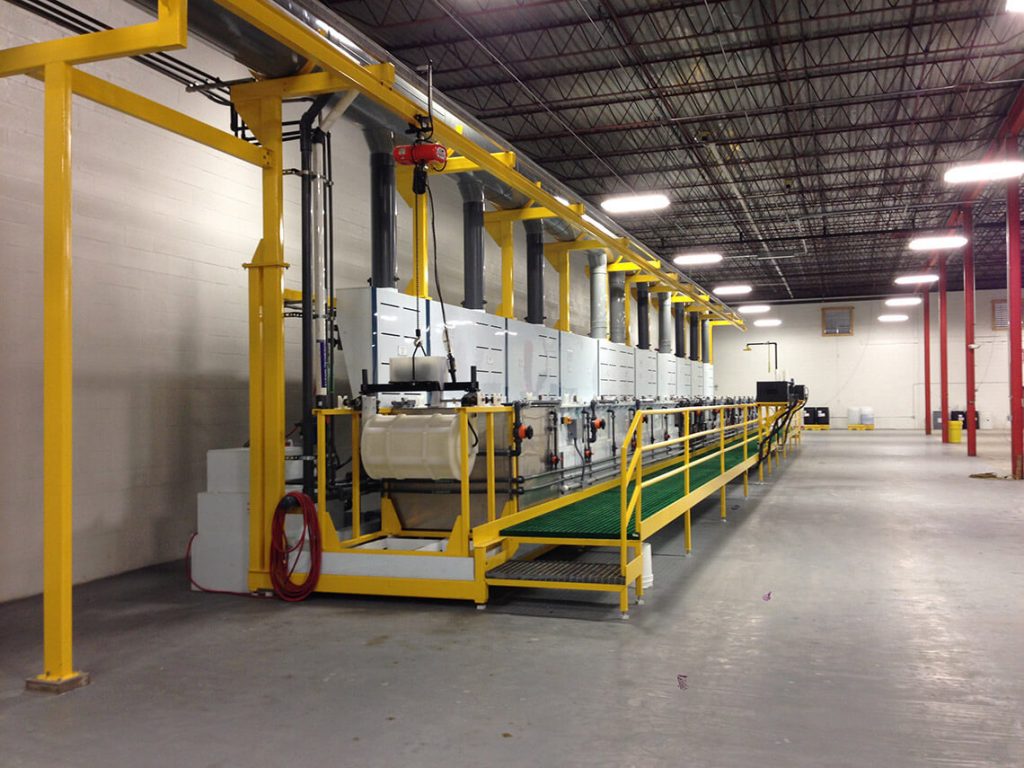
The LHE Zn-Ni plating line at ES3 allows us to test conformal anode performance as well as provide production Zn-Ni plating.
Custom Conformal Anode Design, Fabrication, and Maintenance
The effectiveness of electroplated surfaces, whether for improved wear or corrosion resistance, often depends on achieving very uniform plating thicknesses along critical geometric features of the electroplated part. Recesses, filets, contours, and holes can introduce particular challenges. A well designed and validated conformal anode fixture can deliver very uniform plating thicknesses that are repeatably obtained during electroplating.
ES3 has been providing conformal anodes and custom reusable maskings to the aerospace industry for precision electroplating of LHE ZnNi, Cadmium, TiCd, Nickel and Chrome. Regardless of the plating bath, a conformal anode can greatly improve plating quality and accuracy. ES3 designed and validated the conformal anodes for the Boeing 777 landing gear as well as for the landing gear of other smaller aircraft. ES3 holds several patents and pending patents for advanced conformal anode fixtures. For more information please contact us at plating.info@es3inc.com
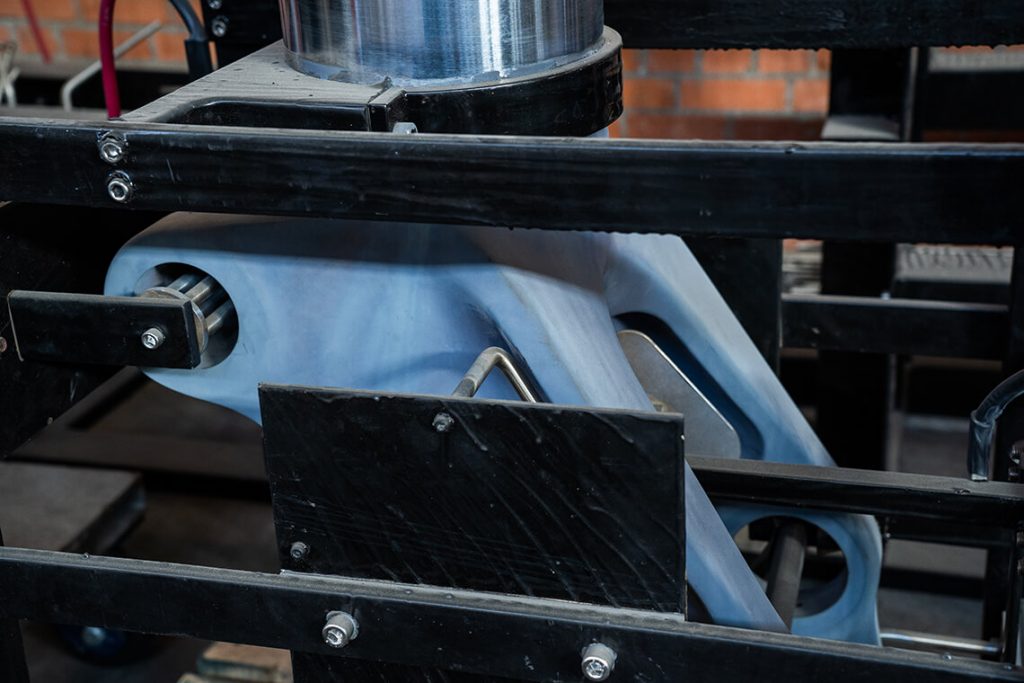
Shown is the B-2 Main Landing Gear Inner Cylinder inside the ES3 designed and fabricated conformal anode which improves electroplating quality and accuracy.